Last updated: June 12, 2024
Article
Assessment of a World War II Blimp Hanger
This is a transcript of a presentation at the Preserving U.S. Military Heritage: World War II to the Cold War, June 4-6, 2019, held in Fredericksburg, TX. Watch a non-audio described version of the presentation on YouTube.
Conducting an Assessment of Wooden Parabolic Arch Trusses in a World War II Blimp Hanger
Presenter: Ron Anthony and Doug Porter
Abstract
Originally constructed for the U.S. Navy during its lighter-than-air program in the 1940s, 17 “blimp” hangars were constructed using large built-up timber trusses that serve as arches. Each hangar is approximately 1,072 feet (327 m) long by 292 feet (89 m) wide by 192 feet (59 m) tall with an unobstructed floor area of approximately 7.4 acres (3 hectares), making them some of the largest timber structures in the world at the time. An initial survey of Hangars 2 at Moffett Field, California, USA, in 2013, which was to undergo adaptive reuse, led to a detailed investigation of the condition of the structural elements of the hangar. The documentation and condition assessment project was possibly the largest condition assessment ever conducted on a timber structure, providing detailed information on approximately 20,000 timber elements.
The timber assessment protocol included:
-
visual inspection of individual timbers in each parabolic arch truss,
-
species identification to determine appropriate allowable design properties
-
strength testing to determine duration of load effects and strength loss due to fire-retardant chemicals after 70 years of service
-
digital radioscopy of split rings and shear plate connections at truss panel points to determine internal condition of the wood and possible corrosion of the steel
-
in-situ visual grading of the lumber and timbers to determine appropriate allowable design properties.
Digital radioscopy was developed, in part, with funding from NCPTT. Digital radioscopy allows for non-intrusive examination of hidden construction and material conditions. The equipment is portable and field rugged, making it practical for historic preservation projects, including examination of bolted connections at the truss nodes. The x-ray source and imaging plate can be positioned to obtain images of complex configurations under a range of field conditions, such as those found in the hangar.
An in-situ grading protocol was also developed, in part, with funding from NCPTT. Lumber grade is determined by species, size of the member(s), and growth characteristics, such as knots and slope of grain. Knots and slope of grain tend to be the grade-limiting characteristics for lumber and timber in older buildings. Measurement of knots and slope of grain on the lumber and timbers making up the trusses indicated the allowable structural grade for each wood member. Knot size and location and slope of grain were measured from boom lifts on all visible faces of individual wood members of the trusses. Documentation of the truss members, including recording survey data, observations, and digital photos, was achieved in real time using hand-held tablets and customized software (Tablet PC Annotation System, or TPAS). This paper describes the development and implementation of the wood assessment protocol using nondestructive testing to determine material condition and behavior.
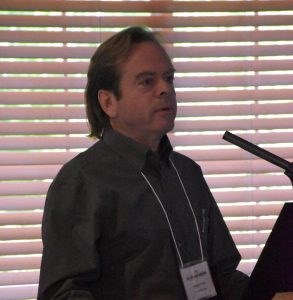
Presentation
Doug Porter: Thanks Mary. I want to start by saying how much I enjoyed that last presentation. I was fortunate to be associated with a research group that worked for about five years on the Pajarito Plateau looking at cavates. And we kind of started with a structural assessment of an ancient wall and ended up focused on case hardening processes that protect the tough outcrops there, and I thoroughly enjoyed the talk about the new park.
Ron and I are going to present on ... what happened to ... there we go, really on one of two blimp hangars that we assessed starting in 2014, I think. Mary mentioned that Ron had been involved with NCPTT in the past developing non-destructive testing technology for use with wood. And we're going to talk about a grading protocol today that Ron developed with funding support from NCPTT, and with some radioscopy technology that was also developed in partnership with NCPTT.
The blimp hangars at the Moffett Federal Airfield are located at the south end of the San Francisco Bay. They were originally constructed in the 1940s as part of the Department of the Navy's lighter-than-air program. In all, there were 17 hangars constructed on three coasts that each made use of these built up arches that form the frame for the hangars. Each hangar is not quite 1,100 feet long, not quite 300 feet wide, and just about 190 feet tall. They enclose an open area of about 7.5 acres, making them some of the largest timber frame structures in the world at the time.

Each hangar was built of approximately 6 million board feet of lumber and timber, the Douglas Fir for the hangars at Moffett we're obtained from different saw mills. They were pressure treated with different fire retardant treatments at different mills and the trusses, or the trust segments were pre-fabricated at different shops. The segments were shipped by train to the site where the two hangars were erected side by side at essentially the same time and using the same processes.
In this image taken in 1943, what you're looking at is a rolling stage. You can see the tracks that this thing moves on. That stage was a work platform and supported the cranes. And I think, right here, we've got a set pre-fabricated truss segment being lifted into position. It will be fastened by workers on that same platform.
Sometime early in the service life of the building, strengthening repairs were made that included nailing diagonal sheathing across pairs of chord members in the trusses, adding bolts to panel point connections. So these connections where web members in chords come together. And then circa 1990, there was a repair campaign that involved installing strong backs on bolt or buckled chord members.
I like this image because it begins to convey a sense of the volume of the space. And I'm having trouble seeing all of my controls up here. There. That's an airplane. That's about the midpoint, or the length of the hangar. These hangars were big enough for nine blimps. Shortly ... or, I'm sorry.
The hangars got a new tenant, and in preparing for adaptive reuse of the spaces, wood inspection protocol was developed to yield information that engineers needed for the analysis of the building. The wood assessment team was a consortium or a put together team that included Ron's firm, a wood science firm, vertical access of ropes, Access Company, and Porter and Associates, a timber framing company. And the three companies supplied the staff for assessing thousands of individual structural members in these two hangars over a period of about three years.
The condition assessment included visual inspection of individual timbers in each of the trusses species ID to determine the allowable design values, strength testing to determine load duration effects, and any weakening of the timber associated with their exposure to the fire retardant chemicals over a period of 70 years or so. Digital radioscopy of split ring and shear plate connections at the truss panel points to determine the internal condition of the wood at those connections, and the connection of the ... or the condition of the fasteners. And then in situ grading of the lumber and timber to determine the allowable design properties. Today I'll talk about the grading. Ron will talk about the radioscopy here in a little bit.
So why grade? Grading is a way to anticipate the strength of a particular wooden member based on the presence or absence of strength limiting defects that are really mostly growth conditions. Knots and slope of grain tend to be the grade limiting characteristics for lumber and timber in older buildings. And by measuring knots and slope of grain in the hangar, and using the information that we collected on species ID and member size, we were able to determine the allowable structural grade for each type of wood member making up the trusses and the bracing in the hangars. The engineers use this information to decide whether the existing frames are up to future design loads.
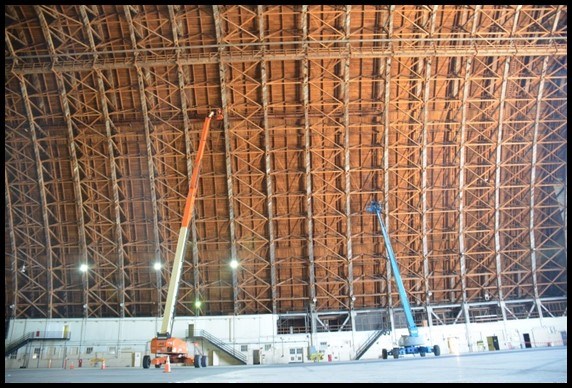
Our teams worked from boom lifts that was partly a result of contamination on the surface of the wood, it meant that rope access wasn't a possibility. That actually, I think, turned out to be a blessing. Working from the lifts, we measured knot sizes and location, slope of grain on all the visible faces of individual wood members in the accessible parts of the hangar. You can see here a truss and a truss. That truss defines a bay in between the pair, and I'm at a bad angle for looking at this but the bay is divided up into cells by bracing. And our routine was to take the bucket of the lift into individual cells and to look at all of the timber and lumber that we could see in each of those cells and to record information about it. But some of the bays had cross bracing at the opening of the cells, and we couldn't get lift into those cells. So while we were working in here, we were looking left and looking right to record information on the base on either side.
Each lift team had two people, one a woodworker or a timber framer, somebody accustomed to working with structural timber. And the other, somebody skilled with the use of the software on the tablet.
We recorded measurements and information on grade and condition, and photographs of individual wood members using a software called TPASS, that stands for tablet PC annotation system. The TPASS database has graphic and numeric components, and the database is searchable for sorting data to recognize trends.
At Moffett knots are the primary strength limiting defect in the lumber and timber. Grading rules specify knot size limitations for knots based on their location. For center line knots on the wide face of a member, these have the least impact on strength, so the least impact on grade, the largest allowable knot size. Edge knots, on the other hand, generally increase localized tensile stresses, and therefore have smaller allowable knot sizes. And in the image that we have here, we are looking at a chord member, a knot that had it occurred on its own would have been a center line knot on the wide face, but it occurs in conjunction with an edge knot. You can see how the grain deviates around not just the edge knot, but right on up past the second knot. And so this would be regarded as a knot cluster having a single, I think that was probably a five inch edge knot that we encountered in one of the chords.
The reason that knots impact, or one of the reasons that knots impact the strength capacity of lumber, is because of that grain deviation, or the distorted grain angle that occurs as the tree grows around the branch. You can get something of the same effect if a board or a timber is milled out of parallel to the grain, or if the log that a timber is cut from has twisted grain due to a spiral growth in the tree.
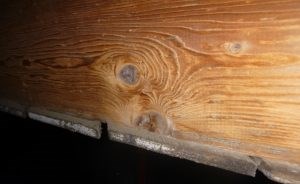
Areas of cross grain or where the grain runs out, concentrates stresses in the wood fibers where they exit the member, and this is what is meant by slope of grain defects. Slope of grain was not such a gigantic issue in the hangars, but we collected slope of grain measurements. Those measurements are essentially a ratio between the distance out of parallel that the grain is from the axis of the timber over a run. And that run usually is 8, 10 or 12 inches, 14 inches I guess. And so as expressed as a slope of grain of 2 and 12, let's say for example.
Contrast the last image with this piece in particular, this is a diagonal web member. So one of the pieces that connects top and bottom chord set and is connected at a big panel point. In this piece, we don't have any defects, and really a great deal of the lumber and timber that we were dealing with in these hangars more closely resembled this piece than the last example.
So this is a summary of some of the results, grading results for hangar two. For a member type to be assigned a particular grade at least 95% of the members need to fall within or above that grade. Many of the member types on our list here come within a few percentage points of making the next higher grade. And whether or not to assign that higher grade becomes a matter of engineering judgment in an existing building like this.
Here's a short summary of our grade findings, and then we're going to get Ron up here. And I guess the interesting things to note about this short list are that the top and bottom chords made select structural, are the highest structural grade that we found in the hangars. They were also the members that our engineering team identified as the critically loaded members in the trusses. Most of the rest of the structural material made number one structural joist and planks. We started out looking for distribution patterns, wondering whether engineers had called out higher-grade lumber and timber for different parts of the trusses. We didn't find that distribution pattern and sorted our results according to member type.
Ron Anthony: I appreciate it. I guess I'm supposed to stand here. Right, Mary? I appreciated the earlier two talks for many reasons, but two of them kind of stuck out. One was the vastness of the cultural landscape, not only the specifics of the Los Alamos sites, but when you look at the Manhattan Project sites, you've got Tennessee, Washington and New Mexico covered in there. And I was fortunate to spend about 15 years working on another part of that story. I love Jeremy's use of the term story. We're trying to tell this story, which I think is what we're all trying to do when we preserve these sites. But I had an opportunity to work in western Colorado near a town called Uravan. Uravan is made up from the two words you uranium and vanadium, and it was a site where much of the yellow cake, the ore that went into the Manhattan Project was produced out of the mining operations there.
I wasn't working on the Manhattan Project aspect of that, but predating that, some gold mining operations in the area. And that area, that cultural landscape, transformed into a mining site where a lot of this ore was then produced. And it's part of that story, as Jeremy would say, that is probably very important when you talk about the Manhattan Project. Things that we maybe didn't know, or were not communicated very well. I mean in the store, in the town of Uravan, they sold yellow cake butter. All the buildings were built on mine tailings from the uranium operations. So all those buildings are gone now because they were too radioactive for us to even preserve. And anyway, that's a different story. Let's get back to this. Everybody's right, you cannot see that screen from up here very well.
Doug talked about some of the work related to grading, and it was an awful lot of work that went into that. In that hangar that he was showing, there are about 5,000 sticks of wood that were graded, so the knots, the slope of grain, whatever other defects were there were measured individually on 5,000 sticks. Those are documented in a database. If you asked me on, and there are 51 arches in a hangar, if you ask me on arch number 27, and you named a specific location from L to M, the diagonal that goes from the top chord to the bottom chord. What is the largest not in there? We have that in a database. It's an incredibly detailed database. So that was the grading operation, and as Doug pointed out, the grading protocol that allowed us to do that, and use that information, allows you to use that, was in part funded through NCPTT.
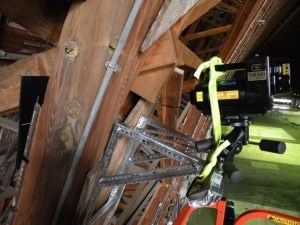
Another project that was funded in part through NCPTT was the use of portable x-rays, digital radioscopy for investigating historic structures. And my focus as a wood scientist was on the timber part of that. And so the radiation that we're using here is totally unlike everything that the previous presenters talked about. These are x-rays that are generated by a cathode ray tube, much like a dental x-ray. In fact, it has about the same energy. What you're looking at in this image, you see an x-ray source, it weighs about 10 pounds, it's operated by a 14 volt DeWalt battery and we're operating in the hangar. And so at this point we're about 80 feet above the floor. And so we had to develop a mounting mechanism that would not cause my heart to skip a beat when we put, you know, $10,000 worth of equipment, 80 feet in the air, if it fell on the ground.
So you can see the yellow strap, that kind of is our safety chord, that if it falls off of the tripod, we have something to catch it before it goes to the ground. But that shows the source. And we're shooting through something here. So this is what Doug called a panel point. You can see we have a number of bolts that are on this member. Each one of these truss elements is made up of dimension lumber. So this is not heavy timber, it's a very large structure, but it's dimension lumber. Dimension lumber can be up to four inches thick. So many of these members were like 4X12s, 4X14s, and multiple pieces put together. So it's a rather flimsy structure, which makes most engineers a little bit nervous. In this case, we wanted to know a number of things. The grade information that Doug talked about, but the engineers were very concerned about the connections.
They said, geez, you got a lot of bolts in there. And we have some drawings, and they have some special connectors in there, things called split rings that increased the capacity of the joint by tying the two pieces of timber together, or tying two pieces together. In this case, we have many pieces of timber, but we know that they did supplemental repairs, as Doug pointed out, at some point. And that included adding some bolts, and so the question was, how do we know if this was built the way that it was intended to be built based on the drawings? And part of that comes from the fact if you put yourself back in the timeframe, this is during World War II, there's a tremendous amount of effort to push ahead and construct these buildings. And they got the material there. It took them about nine months to build one of these, that's a fairly short period of time.
It took me 14 months to build my house. Took them 19 months to build one of these hangars. So you kind of put that in perspective and you wonder, is everything there that needs to be there? So here we have the source looking through one of those. Then on the backside, this is an imaging plate, it captures the x-ray. That x-ray source is a pulsed x-ray machine. So it has bursts of x-rays that come out at 60 nanoseconds. So it's a very short duration pulse, 150 KV source. And then you put an imaging plate on the backside, however you can. And you can imagine logistically, now I'm 80 feet in the air, I'm in a lift, and I have to position this on one of those joints. It's not like a nice piece of something in a laboratory where we can put it on the back of a wall.
I've got a bunch of timbers coming in, I've got bolts. It's very awkward to try and put it into position where you want. But nonetheless, you position that plate. And in a very simplistic way, this is the kind of thing that you get. So if you look at it visually, here's the washer and the head of a bolt going through a piece of wood, and then the image on the right is the radiograph of that image. And you can see, all right, that's relatively straight forward. You've got the darker part, that's the bolt, and you can see the bolthead, that's pretty straight forward.
Well that's not typically what we had when we were out there. We were interested in things like corrosion. We're interested in the condition of the metal. Not only was it there, but was it corroded? The engineers wanted to know and have we lost section in the metal? So you can see on this the threads of the bolt. So we have very little corrosion, if there's any there at all it's surface corrosion on the bolt. The up and down lines that you see in there is the actual grain of the wood. That allows us to determine that we don't have voids in the wood. It would be somewhat amorphous if the wood had been deteriorated.
So when you're looking at a single bolt, or a single piece of metal in a piece of wood, it's relatively straightforward to do that. We had an opportunity to pull a few bolts so that we could identify that. And you can see on this bolt just above the threads, if you look closely from where you sit, it's neck down ever so slightly. There was a little bit of surface corrosion. We could pick that up. The engineers weren't concerned, they were concerned if this was down to half of the cross section, or a third of the cross section. So the only corrosion that we really is surface corrosion, except where the bolt head and the nut were exposed on the outer part.
So I showed the image of the single. Mary, I'm not sure, are you adding more time, or are you ... keep going, okay. So I showed the image of the single bolt. That's pretty straight forward. But on these panel points we had many connectors. All right, so if you picture this, there's a piece of lumber in the joint that we're looking at here. There's a piece of lumber, then there's another piece of lumber, then there's a gap. Then there's another piece of lumber, another piece of lumber, okay? And within those we have the member coming in from the right. That's one of the web members in the truss. So what we're looking at, this more or less vertical member, that is the top quarter of the truss. And then we've got all these other members coming in, each one having a bolt. Some of the bolts are more in what we would call the foreground, some are in the background, some of them are supposed to have split rings. Some of these are repairs which we don't know have split rings.
So you can imagine from the standpoint of taking an image of this and interpreting that. While it's relatively simple, when we go to these next few images, it's a little bit complex in the setup. In fact, the bulk of the time is setting this up so that you say, when I take this image at this angle, I would expect to see three bolts or four bolts. I would expect to see two split rings. So you're looking for certain things in there to try and verify the as-built construction, as well as the condition of the wood and the metal in there. So schematically, what I just said kind of is shown with this. Here's our x-ray source. When we take the image, it's like taking a photograph.
If I have a bolt that's more in the foreground, it casts a larger shadow than one that's right up against the plate. So in other words, they look like different diameter bolts. They're not, they're the same diameter bolt, but it helps us determine the position within the joint, that 12-14 inches of depth. It allows us to determine where those bolts are, and we can identify if there is one with corrosion, which one is that? And this is part of the technology that really came from the research funded in part through NCPTT. You can see that here on this bottom, the very lowest bolt looks like it's smaller than the one above it. It's not smaller, it is just closer to the imaging plate at the back of the image. The larger one casts a larger shadow. Interesting in here, we're seeing that with multiple split rings as well. We know it's a split ring. You can see ...yeah, right down in here. Split Ring, it's a ring that's separated. They cut a groove in the two pieces of wood, put that split ring connection in there. When they tighten it up with the bolt it holds the wood together, increases the capacity by about a factor of two. But you can see we have many split rings. They come in different sizes. We were able to identify the size. It's not that many different sizes, but the engineers were saying, what do we have in there? And this allowed us to gather that information for the structural engineers.
This better shows that depth of the image effect. When you look at these split rings here, we've actually got three split rings. The two on the top and bottom are in the same plane, they're the same distance from the imaging plate. The one in the middle, that one is actually closer to the imaging plate, it casts a smaller shadow. So we can look at visually, look at the joint that we're setup on. Look at the radiograph and tell, yes, we have the split rings in there, they're supposed to be in there. We can see the condition of the bolt. There is no corrosion on a split ring. There's no corrosion on the bolt, there's no corrosion of the threads. All of that is not visible to us, but it is visible through the radiograph.
Just another image, same kind of thing. And I point to, there are things that show up in these images and we kind of wonder what they are. And down here you see there's a faint line going across at an angle. Okay? So you see things like that that show up. It's actually two lines there. There is an upper line, and then there's a lower line, if you can see that. And sometimes you wonder, well what is that? So you look at, visually, you look at the joint on the chord, and then you look at the radiograph and you're trying to figure that out. Here's a better picture of that, where we had this diagonal going across here. And at first you say, what is that that I'm looking at? Go back to that very early image that Doug showed where they had some reinforcement added to the trusses to the arches. Shortly after construction, they put that diagonal sheathing in. That diagonal line that we're looking at here is one of those pieces of diagonal sheeting, so it's a one inch thick member. And it just shows up in the radiograph, but when you look at it on the image, if I didn't know what was in the field, I wouldn't be sure what that was. But we were able to confirm that that's really a piece of that sheeting.
So there's a lot of information contained in here that tells us about the construction, the as-built construction, as well as the condition. There was supplemental strengthening in there, they added these bolts. We know that those bolts that were added did not have split rings. We wouldn't have expected them to, but that allowed us to differentiate between, this is original construction because it has a split ring. This is a supplemental repair because of the lack of a split ring.
There was no severe corrosion on any of the bolts, washers or split rings embedded within the wood. No loss of strength due to that reduction in cross section, because there wasn't a reduction in cross section. The buildup scale visible on the outside could be cleaned off, and the engineers were not concerned about that at all. The clarity of the wood grain and all those images tells us there's no deterioration inside of the wood. It's all nice, clear material. The wood surrounding the bolts, split rings and sheer plates. No visible deterioration on the outside, but more important, no deterioration detected on any of the radiographs.
So both of these technologies, the in situ grading and the radioscopy, again, were supported in part by research from NCPTT. And I say that because it's critically important. Some of this stuff can't get out there for us to use. All of this is available to you use, you can download the report. It's all there. We picked two aspects. The research and the investigation that went into the blimp hangar was much more detailed than any of this, but I thought it was beneficial to show you how some of the NCPTT research plays into this. And with that, are there any questions?
Questions
Mary Striegel: Let me get to the questions.
Speaker 1: So with your radioscopy images, did you also have a normal photograph that went with it so you can kind of use the two to compare, so you could see what's going on with it better?
Ron Anthony: Yes, and that's a very good question. Because when you're in a field, you can imagine many of these, if you take the lift, either one of these, you're 40 feet off the ground, or your 60-80 feet off the ground in these two lifts that we see in this image. So you're up there and you're setting at an angle because the member's not vertical, it's curved, it's an arch. So you focus the imager and you focus the source to try and shoot through a particular angle. If you take that image and you go back to the lab and you try and study that without knowing how was it set up, you're totally lost. And that's part of the setup. And so what we would do is we would place on top of the source, we would place a digital camera and take an image so that visually it's looking at exactly the same angle that the x-ray source is shooting through so that we would have some reference point back in the lab.
Speaker 2: Yeah, real quick. When he was talking and showing some of the 90’s repairs, of reinforcements, it looked like it was non-treated lumber, versus the treated lumber that it was built with. Did you find that over time when they did replacements they weren't using treated versus non-treated lumber?
Ron Anthony: Well, that's a whole other paper. But those strong backs that Doug showed in the image, they had some either buckling in the trusses. So the entire truss, if you looked at it would be out of plane, or they had some failed members. And so a fellow by the name of Don Neil designed these repairs, and it was a logical approach. And what he did was he said, the trusses are not stiff enough, so he wanted to increase the stiffness by about a factor of six. So he did that using glue laminated timber that he put on the side. And for those of you that are engineers in the room, you could maybe see by increasing the localized strength and stiffness in one point, you were changing the load path. And so that's exactly what happened in much of this. He beefed it up so much that the load found another way to go, and then we had unintended consequences throughout the hangars because of that. But he was using non-treated Glulam for those particular repairs.
Speaker 3: I have a comment and a question. I think that using pulsed x-rays on a structure like that is really interesting. It's very portable. It's highly calumniated, so you don't take a lot of risk as much as when you are using an x-ray tube. And an x-ray tube is out of question because it's too heavy and requires a different setting. So I think that this is a really wonderful technique for looking at relatively low density materials. However, I would have probably looked at using a different unit, probably a 200 or 300 KV unit. I think that you would have maybe seen more about the corrosion and the ... I don't think there is any corrosion on these. I agree with you, but a 300 or at least 200 KV would have been interesting. Have you tried one?
Ron Anthony: Yes and no. Okay. So yes, I use a stronger unit and using that on wood it overpowers. So I mentioned it's a 60 nanosecond pulse. It's a very short duration burst. And if I'm looking at a piece of wood, I may only use one or two pulses. Even through these joints I might only use 4-6 pulses, and that's with 150 KV. So I did look at when I wanted to go through something thicker, and I've done similar work on masonry, I'll use a higher voltage in there. This is something everybody in the room that does anything related to preservation recognizes. We don't have the luxury of developing this kind of equipment for ourselves. We have to take what's out there and adapt it. So this equipment was actually developed for defense purposes, so it was used for military and police operations and a lot of that.
And so, I said, I wonder how I can adapt this to wood? And the source is manufactured by an outfit called Golden Engineering. And I worked with them very closely, and they recognized this isn't ideal for what you're trying to do on these buildings, but it's what we sell. We could make you another one and that would be X hundred thousand dollars. And in the preservation field, when somebody talks about spending X hundred thousand dollars to develop a prototype, we typically don't go down that path. So I would have done things different if I'd a had another funding source that would pay the bill for that. Because yes, it could clearly be improved from what we've got here.
Speaker Bio
Ron Anthony, wood scientist, received an M.S. in Wood Science and Technology from Colorado State University. Prior to forming Anthony & Associates in 1999, he conducted research and consulted on wood properties and the use of wood in construction applications. Mr. Anthony’s research activities, several projects that have been conducted through NCPTT, have focused on nondestructive evaluation and materials testing to better understand how wood interacts with other materials and performs over time. He participates in historic preservation projects, conducts forensic investigations, and assists with timber design issues. Mr. Anthony is the 2002 recipient of the James Marston Fitch Foundation Grant for his approach to evaluating wood in historic buildings. He is a Fellow in APT International and the 2018 recipient of APTI’s Harley J. McKee Award.
Doug Porter, an architectural conservator, focuses on investigation, stabilization, and repair of culturally significant sites and structures in cooperation with academic, federal and non-profit partners. Projects involve condition assessment, materials analysis, structural modeling, laboratory and field-testing of conservation treatments, and treatment implementation. Porter holds a research faculty position in the School of Engineering, University of Vermont. He is on the Board of Directors of the ICOMOS International Scientific Committee on Earthen Architectural Heritage (ISCEAH), and an expert member of the ICOMOS International Scientific Committee on the Analysis and Restoration of Architectural Heritage (ISCARSAH). Recent projects include assessment and repair of the Lost Horse Mine and Mill (CA), the Reiling Dredge (CO), the Bartlett Cabin (NM), the Silver Bell Mine (CA), the Live Oak Mine (CA), trestles at Golden Spike National Historic Site, (Utah), Keane Wonder Mine Aerial Tramway (Death Valley National Park), Cable Mountain Draw Works (Zion National Park), and the Breeding Barn at Shelburne Farms (Vermont).
Read other articles from this symposium, Preserving U.S. Military Heritage World War II to the Cold War, or learn more about the National Center for Preservation Technology and Training.