Pueblo potters still use traditional methods to make pottery. In the past, women generally were the potters, but today there are many fine male potters as well. The pots below were made by Legoria Tafoya, illustrating the steps used to make Santa Clara black pottery.
Tafoya digs clay from a place known to her family for generations. She soaks the clay, and removes impurities such as stones and leaves. In most pueblos the clay needs temper in order to fire evenly and not crack. Some pueblos use local sand. Others grind basalt [a dense, hard volcanic rock] or broken pieces of pottery into fine particles.
The clay is usually left to "rest" overnight. A small piece is shaped into a ball and flattened into a disc. It becomes the vessel bottom. Long strips of clay are coiled around and around to build the pot's body. The potter pinches the coils together and then scrapes the seams smooth. She does not use a wheel. When the pot has reached the desired size, the potter pulls, pushes, and scrapes the walls to the needed shape. She uses rounded pieces of gourd to smooth the pot inside and out. If the pot is for everyday use, the pinch marks are left on the outside, and only the inside is scraped smooth. The pot is then dried slowly to prevent cracking. The potter burnishes the surface with a polishing stone or cloth to produce a gleaming surface.
A slip of fine clay is painted onto the pot to form a canvas for the design elements. Yucca paint brushes are still used to apply mineral paints to create design elements. Pueblos use distinctive color slips. Cochiti, uses creamy white, and Acoma and Zuni use bright white. Each pueblo has its own designs and forms, as do individual potters.
The pot is then fired outdoors, using wood or manure as fuel. A good fire and sufficient oxygen yields the best results.
|
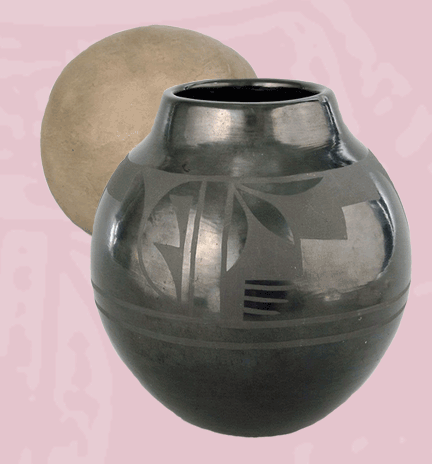 |