In mid-August 1959, the EODC was in midst of reviewing the plans, and
bidding on the visitor center and cyclorama building opened September
29. The contract was awarded to the Orndorff Construction Company, Inc.,
of Camp Hill, Pennsylvania, for its bid of $687,349, an estimate $45,000
less than the second lowest proposal. [30]
Total construction time for "one of the largest buildings in the way
of Visitor Centers to date" was projected as a single year; it was Director
Wirth's particular hope that the building could be dedicated while President
Eisenhower remained in office. [31] The project's
four primary contractors officially began work on November 18, though
the electrical, cooling and heating, and metal workers awaited Orndorff's
preparation. [32] Within a few days, the construction
company had a tractor trailer at the site and inspectors checking elevation
lines established by EODC Engineer Westerfield. According to the contract
specifications for the visitor center, the rotunda was to be prepared
for installation of the cyclorama painting within just one hundred and
eighty days. To meet this tight deadline, the contractors were advised
to give priority to the construction of the concrete drum. [33]
After excavating a footprint 130 feet in diameter and digging spread
footings, contractors began driving piles for the rotunda foundation.
They were surprised to find that the rock did not meet required standards;
in fact, it didn't appear to be the same material obtained by prior
tests. Upon further investigation, the contractors discovered the building
had been moved about twenty feet since the initial foundation inspection.
During their December 17 site visit, the architects hired an expert
to analyze the situation. Robert J. Stickel, a civil engineer from Camp
Hill, Pennsylvania, suggested shifting the building an additional twenty
feet to the east. [34] Throughout these inspections,
the construction company insisted it could "do nothing until the center
pivot point was established by the survey crew." [35] By January 1960, Neutra and Alexander had revised the
foundation plan. Over the next month, the remaining footings were custom
designed to suit their varying site conditions.
In early December, Neutra and Alexander congratulated the Orndorff
Company for recognizing the "national importance" of the future building.
[36] The architects had received the contract
to supervise construction of their design, and it was in their best
interest to anticipate mutual cooperation in the work ahead. [37] Over the next few years, both principals of the firm
would visit the site many times and respond to everyday questions by
mail and telephone. Dion Neutra remained based in Los Angeles, but represented
the firm in official correspondence and on many site visits. [38]
Weekly supervision of construction was undertaken by one of Richard
Neutra's former assistants, Thaddeus Longstreth, who had since opened
a private architectural practice in Princeton, New Jersey. As the firm's
"eastern representative," Longstreth maintained a weekly record of construction
progress, logging nearly one hundred supervisory reports between November
1959 and March 1962. He focused on "the interpretation of the plans
and specifications from an architectural and aesthetic viewpoint rather
than the mechanical aspects of the building." [39] Technical matters were the prerogative of subcontractors
in California, including mechanical engineer Boris M. Lemos, electrical
engineers Earl Holmberg and Associates, and the firm of Parker, Zehnder
and Associates, consulting structural engineers. In addition, the project
was under scrutiny by David O. Smith, the project supervisor. Although
a Park Service employee, Smith acted as a liaison between the government
and the architectural firm. The highest authority in the Park Service
with intimate knowledge of the project was John B. Cabot, supervising
architect of the EODC in Philadelphia, but even Cabot declared Gettysburg
Superintendent James B. Myers the official "owner" or client. Along
with these overseers, the crowd at the construction site included Willard
Verbitsky, a 340-pound superintendent known as "Little Willie" by his
co-workers at Orndorff Construction. Both John J. Bordner, vice president
of Orndorff, and President Brickley S. Orndorff stopped by to check
on progress and handled the project's substantial correspondence with
its west coast designers. The construction company hosted an introductory
dinner for the group on December 17, 1959, a few weeks after work had
officially begun.
While the foundations were under scrutiny, the architects turned their
attention to sample panels of the stone walls. Although the requirements
for the stone masonry may have appeared stringent, the contractors had
been forewarned by the building specifications, which stipulated every
detailfrom the three sample panels to the provision of a local
example for the mason's examination. [40] The stone required in the specifications was native
"'Arcure' Pennsylvania Sandstone in the tan, brown or buff color range."
As the architects explained, the most aesthetically pleasing masonry
pattern consisted of "darker and larger stones . . . nearer the bottom
of the piers and color and size graduating toward the top to lighter
and smaller pieces." [41] They also indicated
that the sides of the piers as seen from the east were most important
and that the very best stone should be reserved for the four piers nearest
the entrance. [42] In preparing the sample,
Longstreth and the contractors explored the surrounding area for historic
examples of the desired "random rubble ashlar pattern with more irregular,
triangular shapes." [43] The Vickery Stone
Company of Upper Darby, Pennsylvania, dumped approximately 155 tons
of Blue Mountain split-face Pennsylvania sandstone at the job site on
February 25, 1960. The architects hoped to have the panel erected by
December so that it could weather over the winter. [44]
Despite efforts to get off to a friendly start, the foundation problems
inspired more doubts than confidence. When construction was still in
its infancy, the architects warned Orndorff not to substitute less expensive
or more accessible products for those specified in the contract. Neutra
and Alexander insisted they could "not accept very much deviation for
design reasons." [45] The firm's adamant adherence
to specifications became a problem for the contractor because high-quality
products were difficult to obtain; both parties disagreed on what they
considered suitable substitutes for specified items, and such commitment
to high standards resulted in countless delays. For example, the architects
selected expensive Japanese tile distributed by a Los Angeles dealer
to cover the inside of the cyclorama ramp. [46]
This decision not only resulted in considerable delays, but evoked disapproval
from those committed to the Buy American Act. The fact that the architects
supervised construction undoubtedly helped the contractors understand
the complex project, but it also allowed the design process to extend
into the construction phase; the designers could not resist enhancing
the building's aesthetics whenever possible. Rather than simply directing
installation of the original tile, the firm continued to imagine new
effects, envisioning "a mixture of two closely related shades of dark
brown or black, perhaps alternating vertical strips to give a very subtle
corduroy-like effect as a backdrop for the stainless tubes" and with
a matte glaze to prevent any "glitter." [47]
Regardless of additional time or expense, the architects based decisions
on aesthetic issues and structural considerations that might effect
the performance of the building. While such practice resulted in exceptional
quality, the contractors and subcontractors were sometimes baffled by
what they interpreted as capricious decisions.
When the spring building season began in early March 1960, the foundations
were in place, and the architects focused their attention on concrete
forms. Once the outer form work for the rotunda was finished, pouring
began. The first pour was completed in sections between columns. The
contractors worked their way around the circle, leaving space for the
auditorium doors, and then moved on to the next vertical wall segment.
Scaffolding was erected to hold workers and concrete in place as the
layers of lifts accumulated. The rotunda's inner form was begun in August,
and as construction progressed, it advanced in height along with the
exterior. Photographs of the unfinished concrete shell in September
show a fortress equally as impressive as the final product. The remaining
wood scaffolding, with its tiny ladders still climbing up the side of
the building in December, gives a sense of the incomplete rotunda's
huge scale; in contrast, the finished form would ultimately succeed
in dissolving into the grove, at least as much as could be expected
from such a massive shape. The cylinder was of ribbed concrete, a decorative
vertical pattern that required precise formation.
In the same way that Neutra and Alexander insisted on perfecting the
rough and random look of the stone masonry, the architects were determined
to achieve a "crisp and clean" contrast in the concrete. The aesthetics
of both interior and exterior could suffer from shoddy form work, careless
concrete preparation, or improper pouring. Although Park Service project
supervisor David Smith warned against using prefabricated plywood panels,
the contractors objected to the expensive 1- by 6-foot shiplap required
in the specifications. [48] In a letter to Orndorff, Dion Neutra explained why
seemingly insignificant details of the concrete process were aesthetically
important and mentioned similar techniques used by other architects,
such as the "Unesco Building in Paris and any recent work by Le Corbusier,"
to illustrate his point. [49] Such modernist buildings used concrete to create "pure"
forms without any suggestion of their fabrication. The capacity of concrete
to take on a smooth, sleek appearance in a variety of shapes was the
very reason it became a featured material of modern architecture. The
cyclorama ramps under construction might prove expensive and challenging
to design properly, but they would also contribute to the building's
streamlined aesthetics. Chamfer strips were removed from exposed corners
because they made "the building look clumsy and warehousey rather than
sharp and crisp." [50] According to Dion Neutra, such attention to detail
was "why the Park Service went west for their architect, and why this
will be a distinguished building with all of us working on it, dedicated
to this proposition." [51] The firm finally
compromised by allowing plywood forms in unexposed areas, such as the
inside curved surface of the mechanical room and the portion of the
rotunda hidden by the painting. Some covered areas, the outside surface
of the central drum in particular, required shiplap to produce "a true
curve." Although the firm anticipated a certain amount of rubbing out
of form lines, they preferred to "have as little patching or rubbing
as possible, but rely rather on the best form work to avoid problems."
[52]
As Neutra and Alexander and contractors debated the importance of proper
form preparation, they also confronted deficiencies in structural concrete.
The concrete columns in the main rotunda, alphabetized from F to Z,
each required proper footings and piers. Park Service supervisor David
Smith reported on defective concrete in the main R column that extended
from the foundation to the support of the cyclorama drum; Longstreth's
construction report described the problem as "stone pockets" that compromised
the density of material. [53] The architects immediately demanded the removal and
replacement of the column. They were alarmed "to think that these results
are being obtained on a building that will depend in such large measure
on the quality of its concrete finish." [54] Later that month, the adjacent T and S columns were
discovered to be equally faulty and also required removal. [55]
Upon further inspection, it was determined that the "honey-combing and
stone pockets" resulted from the failure to adequately vibrate the concrete.
Soon after, Smith reported "errors" in the footings and asked for suggestions.
Toward the end of April 1960, he agreed to make a surprise visit to
the concrete mixing plant to take test samples of sand and aggregate.
[56] In the meantime, Brickley Orndorff promised to write
the company with his complaints. Flawed concrete preparation, usually
a result of improper vibration, plagued contractors and architects alike
for the duration of the project.
Despite the construction problems, "the Lincoln Memorial at Gettysburg"
was included in a profile of the firm by Pacific Architect and Builder
in May 1960. An aerial view of the building from the entrance facade,
rendered in pastels or watercolor, showed the three reflecting pools
darkened and the rotunda dwarfed by surrounding trees. The short description
of the building noted that it was under construction "on the famed battlefield
some 200 yards from where President Lincoln made his speech," and stood
"only a stone's throw from the horrifying spot where the contest found
its climax." The location of the building was clearly considered an
admirable quality. [57]
The architects returned to the aesthetics of the stone masonry piers
and walls in mid-April 1960, when a sub-contractor began work on a second
sample panel. During construction Longstreth deemed the panel too similar
to the initial rejected attempt. The frustrated mason described his
previous success erecting stone walls for the National Park Service
at Camp Green Top (Catoctin Mountain Park) in Thurmont, Maryland. Longstreth
visited the park, only to find that the walls in question were "too
polychrome in range with a preponderance of square shaped pieces." [58]
After Cabot and Neutra inspected the work the next month, they accompanied
contractors to an old barn on Route 116 west of Gettysburg. A corner
of the structure exhibiting the desired variety of stones and mortar
thickness became the example for visitor center masonry. [59]
On June 21, Longstreth and Bordner traveled to the Blue Mountain Stone
Quarry ten miles northwest of Harrisburg in search of stone that might
cut into satisfactory shapes. They discovered two potentially useful
types of stoneone with a "regular" effect when cut and the other
likely to form "larger irregular shapes" but too gray in color. [60] The quarry owners were so sure of success that they
volunteered to construct a product sample for the architects' approval.
Longstreth and Smith then accompanied them to the exemplary barn to
see the desired stone pattern. The next week, the quarry owners erected
the sample from stone on the site supplemented with their own Blue Mountain
stone. Longstreth reported that this panel "showed great improvement
over previous efforts, having more irregular shapes, thinner dry-wall
appearing joints, larger and darker stones at the base." [61] Nevertheless, he felt that the nature of the rock still
hampered efforts and further construction would require constant supervision.
He hoped that the principles learned while building the samples could
be transferred to the field, allowing the masonry covering the sides
of the rotunda's external concrete piers to become "fieldstone panels."
The five piers nearest the main entrance extended beyond the edge of
the rotunda and created a platform for the concrete cylinder.
Once the mason had actually erected part of pier R and column P, Longstreth
commented on the lack of color variation; tones were supposed to graduate
from dark on the bottom to lighter nearer the top. He also demanded
thicker, darker stone for the panels, noting that the thinner stone
might be reserved for the center of the walls. The stones were to appear
naturally chunky and randomly selected, but the wall itself required
proper alignment. In terms of pattern, Longstreth asked the mason to
avoid "uphill joints" or stones laid too vertically. The mason was to
begin with the least visible piers, such as the north side of pier Q,
before moving on to the featured south facade. [62] During supervision of the pier work in early November,
Longstreth warned the mason of "downhill joints," and suggested that
he constantly stand back from his work to avoid such monotonous effects.
Although larger and wider stones were now in use, the color range was
still disappointingly small and the joints too horizontal. Given the
range of colored stone provided and its varying appearance when split,
Longstreth felt that only constant effort would achieve the desired
results. [63] By this time, John Cabot had given
Longstreth full authority over this aspect of the project. [64]
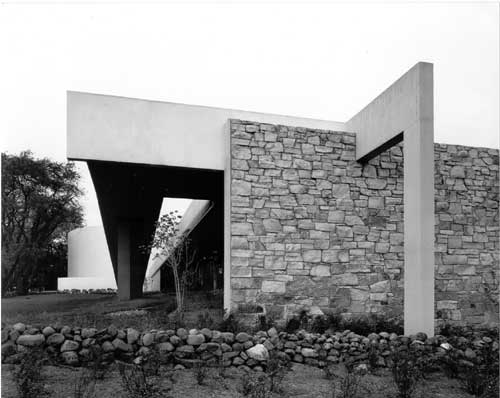
Figure 35. Stone panel and stone
wall on the south end of the office wing, 1962.
(Photo by Lawrence S. Williams, Inc.)
|
In the fall of 1960, as work began on the interior surfaces of the
building, aesthetics took precedence once again. When Orndorff submitted
vinyl wall covering for the office partitions, the architects were horrified
by samples that "might do in a bar or club, but not in this type of
structure." [65] They also disapproved of
the wood sample panels, noting "the dust and pock marks, as well as
the too-glossy finish," a result far different from the sought after
"satin, even, low sheen, full bodied, rubbed effect." As for the colored
concrete required in the exterior ramp, the architects preferred the
chocolate color supplemented with abrasive additives for additional
texture. Orndorff sent three samples sealed differently but all including
sidewalk grain chips, and not very tactfully indicated that the architects
had now received "the full range of the colors as manufactured by A.
C. Horn." [66] The next week, the architects
reported the lack of any attempt to use silicon carbide (alundum grains)
to create the specified textured surface. [67] To complicate matters, the exterior ramp required extensive
structural revisions. While the architects complained about the contractor's
interior selections and form work, the Park Service blamed the architects
for a five-month delay in submitting a finish schedule. [68]
Even as they exchanged complaints, however, all parties pressed on.
Orndorff scheduled terrazzo work in December, beginning with the ground
floor lobby and restrooms, continuing to the second floor office wing
and then entering the cyclorama. [69]
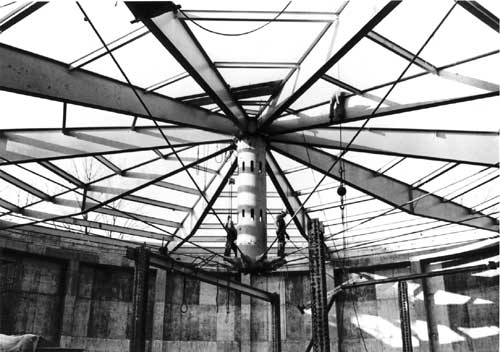
Figure 36. Gettysburg Visitor Center
and Cyclorama, view of the roof structure under construction, December
1960.
(Courtesy National Park Service Technical Information Center,
Denver Service Center.)
|
During the slow and difficult interior design phase, work on the cyclorama
roof proceeded quickly and relatively harmoniously. In a September 1960
report to the architects, Parker, Zehnder and Associates explained details
of the construction joints for the cyclorama beam, wall, and floor.
The appearance of the concrete forms changed significantly in October,
when contractors began to erect steel girders and beams for the rotunda
roof. Two cranes were required, one to place the cyclorama roof steel
and another to lift the concrete for the interior columns. Project Supervisor
Smith updated the architects on conditions at the site and described
his view of future progress:
As it stands now, the center post is solidly supported
2' above the final elevation and 6 girders from J clockwise . . .
inclusive are attached. After the cyclorama wall is completed, the
other four beams and purlins will be erected and the cables connected.
I assume at this time the blocking will be removed (although I see
no provision such as wedges to do this) letting the center post settle
to its final elevation. I assume this is the correct point in the
installation for the welding of the beams to the center post. [70]
Neutra visited the site around Christmastime specifically to photograph
the interesting spiderweb pattern created by the rotunda's exposed steel
framing and endured "great pains and great physical discomfort" in the
process. [71] According to Smith, the revealed
roof structure had already attracted much attention. The Bethlehem Steel
Company took pictures of the cyclorama drum and roof structure for a
full-page advertisement and brochure publicizing its bridge cables.
The rotunda roof was built around an 18-foot center column suspended
with steel purlins radiating outward above a system of "prestretched
and proofloaded bethanized bridge strand." [72] The bridge cables were attached to the base of the
central column and to the upper perimeter of the cylinder, forming a
flexible "web" of fibers. After the erection of the steel but before
installation of the gypsum roof, the cables were adjusted to vertically
align the central column. The framework of purlins and girders above
resembled a wagon wheel. One of the photographs in Neutra's Buildings
and Projects shows two men near the central "trunk" dwarfed by the
steel umbrella overhead. Views were also taken from above the cyclorama,
probably from one of the cranes used in the construction process. It
was a dramatic photo opportunity and one that would soon disappear under
layers of lath and plaster. By the following summer, the roof scuppers
had already become filled with leaves, and Smith planned a regular inspection
schedule to keep the drains clear. [73]
The firm's specifications emphasized their quest for "Architectural
Effect," a subjective standard they strove to achieve through materials,
methods, and even decorative art. Bush-hammered columns formed an important
part of the original interior scheme, and as the project progressed,
this rough appearance became increasingly desirable. While contemplating
the color scheme, the architects decided to leave all bush-hammered
columns in their natural state to expose the black aggregate and reduce
the quantity of dark brown. [74] After the bush-hammering process, columns required
additional work to "remove the spiral form marks and to give surface
variation as called for in specifications." [75] In February 1961 all parties agreed that bush-hammered
columns should be left natural on both the interior and the exterior.
And by the next month, the preference for bush hammering included the
bench surrounding the museum exhibits. The Park Service issued a change
order to reveal the aggregate in the circular museum bench, "upon consideration
of the color scheme for the building, and after seeing the effective
result of the exposed aggregate in bush-hammered surfaces at various
locations in the building." [76] The architects also improved the transition from the
second floor corridor to the cyclorama ramp by substituting stainless
steel for galvanized iron in the bridge spanning the exhibit area. Since
the ramp was enclosed within a stainless steel cage of the same material
and style as the rostrum, this choice unified the metal work in the
museum. The transition plate was actually thin strips of steel with
enough space between to create a dizzying effect when looking down at
the terrazzo floor below. The plate and corresponding balustrade also
provided support for a glass mural.
Just as they imagined the "floating" office wing, the architects conceived
of a dramatic interior with office partitions "shooting on into the
corridor and the feeling of the long vista of the windows continuing
beyond." [77] Demountable partitions of the
"flush movable type" produced by the Neslo Manufacturing Company in
New York separated the office space in the second floor administrative
wing. This system allowed removal of any panel in any order without
affecting other partition walls. The individual laminated vinyl panels
could be taken apart and rebuilt if necessary.
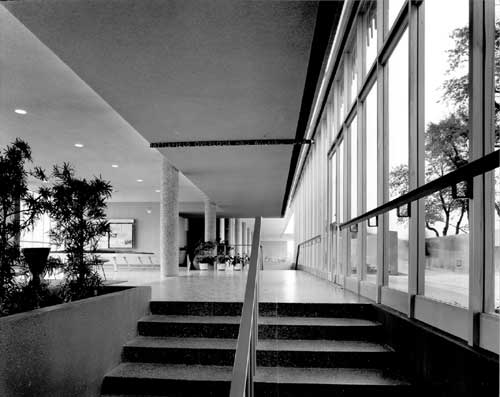
Figure 37. View looking south into
the second floor lobby space, with offices beyond. The ramp up to
the battlefield overlook is visible outside, 1962.
(Photo by Lawrence S. Williams, Inc.)
|
By mid-summer, architects and contractors prepared for work on the
building's unusual solar window shade system. The entire east office
window wall was covered by exterior louvers, which created a pattern
of vertical lines that changed in width as the shades were manually
cranked open or closed. The louvers were fabricated of ALCOA aluminum
covered with a Lemlar primer and two coats of baked enamel finish. As
Dion Neutra explained to the EODC, his father was "recognized as perhaps
the originator of this type of solar control, having first used it some
twenty years ago, when every piece had to be custom made." In 1956,
the firm's Northwestern Mutual Fire Insurance Office (1951) was included
in a book about innovations in aluminum construction. [78] This building is dominated by vertical aluminum louvers
that extend from the 7-foot office windows beyond the spandrel below,
producing a unified front facade. As Neutra reported, the architects
had used the same design in more recent local projects with excellent
results. He may have been thinking of the Amalgamated Clothing Workers
Building (1956) near Wiltshire Boulevard or current work on the Los
Angeles County Hall of Records, which featured "base-to-cornice light
controlling, energy-conserving louvers" constructed about the same time
as the visitor center. [79] In addition to the streamlined vertical lines of the
louver pieces, the architects appreciated their transparency, which
gave a contrasting sense of lightness to the surrounding concrete.
During construction, the architects decided to change from the manual
louver controls to the Lemlar Manufacturing Company's system of automatic
solar adjustments. The park hesitated to spend the extra money necessary
for this luxury, but the architects were persuasive. According to Neutra,
there were practical reasons for mechanizing the louvers. People tended
not to adjust them until they were very uncomfortable and, once closed,
they would usually remain shut since artificial lighting was provided.
This "greater dependence on automation and push-button living" increased
as the world modernized. Dion Neutra sent the park a letter from the
manufacturing company stating that the cost of operating the louvers
automatically would be less than the expense of hiring someone to turn
the hand crank throughout the day. Lemlar suggested that curious park
administrators inquire about the louvers at a milk company in Camden,
New Jersey, where they had been installed in 1957. [80] After some delay due to travel engagements, John Cabot
resolved the situation by explaining the Park Service's hesitancy to
install "mechanical gadgetry." Nevertheless, Cabot was willing to approve
the louvers, if provided with a hand crank for emergencies and the chance
to review additional costs. The company's promise to install the mechanism
itself sealed the deal. [81 ] The Lemlar Manufacturing Company sent their sun louvers
to the site April 27, 1961.
The cyclorama's motorized doors could become an equally dynamic aspect
of the main entrance facade, but they were only intended for use on
special occasions. A portion of the east rotunda was outfitted with
mechanical sliding doors, and a wall of the auditorium operated on a
pivot. When both doors were opened, the museum became a speaker's platform
and the south lawn an expansive seating area. The architects chose the
Ferguson Door Company of Los Angeles to manufacture the motorized sliding
and swing doors. After reviewing the Ferguson Company's installation
and drawings, the architects were pleased with the workmanship of a
complicated, technical project. They looked forward to the "spectacle"
of watching "the doors all operating at once." [82] The next spring, project supervisor Smith reported
that the "pattern sheets" for the Ferguson doors were undergoing a final
adonizing test. The architects advised waiting to install the door panels
until after all sandblasting, Thoroseal application, and plastering
had been completed. [83] Finally, in early August, only a delay in the arrival
of the doors prevented the Park Service from hanging the painting."
[84]
If the louvers and walls only operated at certain times, the building's
water features provided a constant source of stimulation. A few months
earlier, the concrete had been poured for the upper pool on the office
wing roof. This stretch of water extended the full length of the viewing
deck before flowing down to an intermediary pool on the auditorium roof
and cascading to a ground level pool near the visitor center entrance.
The water was kept in motion by a "piped circulation system." According
to the specifications, after the completion of concrete work, a "waterfall
diverter" was required in the intermediate pool to "reduce splash, impact,
and noise to a minimum, as audited from the Projection Room." [85]
Pouring the concrete for the pools was a relatively straightforward
process, but waterproofing them proved more challenging. By June 1961,
a special polysulphide caulking compound was required in the pool joints
to prevent water from leaking into the office wing below. [86] A few months later, the park "noticed that the concrete
slab, placed over the roofing to provide a surface for the view deck,
had moved thereby sheering the deck drains, pulling the cove base away
from its backing and presumably rupturing the waterproofing." Besides
the pool repairs, the adjacent view deck required a quarry-tile walking
surface. [87]
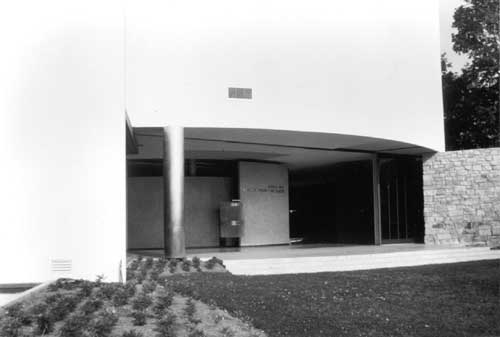
Figure 38. When the glass doors were
opened, this section of the Cyclorama building's drum served as
a stage complete with rostrum. The auditorium doors opened to provide
indoor seating, and the lawn accommodated additional spectators.
(Courtesy Architectural Archives, University of Pennsylvania,
Philadelphia.)
|
As the building neared completion, the consistency, size, shape, and
pattern of stones in the rock walls continued to be a priority. Longstreth
warned the mason to vary the top of the piers with larger, more horizontal
stones. In a letter to Smith, he mentioned that larger, darker stones
should appear at the bottom and suggested looking for proper stone at
the top of the quarry. Superintendent Myers worried about the "dry-wall
effect . . . which would cause excessive moisture entering joints."
This problem could be avoided by packing the mortar more deeply and
inspecting all areas while taking care not to create the "appearance
of a tooled joint." [88] The work accomplished
through the spring of 1961 was accompanied by an incessant aesthetic
critique. In March, stonework was delayed while sub-contractors searched
for additional dark-colored stone. The "triangular chinks" in pier T
were removed and repaired. And the mason was reminded to "avoid repetitious
shapes side by side." When the darker stone arrived at the site, supervisors
complained about the thickness of the pieces. The joints were too wide
and the stones at the bottom too small. By May 3, the south stone was
eighty-five percent complete. In finishing up this important section,
the mason was warned against creating a "quoining effect," in other
words, suggesting a regular termination of the wall at the corner by
using similar square stones. Finally in the fall of 1961, issues involving
the stonework no longer related to the actual stones, but to the color
of mortar joints and the painted ends of concrete piers. [89]
During the spring of 1961, the architects began preparation for the
final stage of the concrete drumthe application of a liquid sealant
called Thoroseal. [90] According to Dion Neutra
and the product manufacturer, success depended on the effect achieved
prior to the application of this final layer. Unfortunately, "the horizontal
pour joints read clearly on the ribbed concrete areas between ribs especially
on the Cyclorama drum, and rear wall of Auditorium and Mechanical. These
must be ground flush afterpatching voids to correct for any possible
variation in plane of one pour to the next. While the ribs will tend
to overpower slight imperfections, there must be no 'ghost' of the horizontal
'bands' now quite dominant in the picture." Before applying Thoroseal,
the firm recommended grinding six inches above and below the visible
joints and performing "heavy sandblasting to effectively remove all
traces of form oil down to clean concrete." [91]
Finally, in May, a product representative of the Thoroseal company applied
test samples of the product over certain construction joints to see
if it would adequately mask surface deformities. According to Standard
Dry Wall Products, the first coating of Thoroseal could be painted on,
but a second coat required use of a plastering spray gun that blasted
a mixture of Thoroseal and white silica sand. [92]
While working with the samples, Gamble discovered "rough bulging patches"
that required smoothing out, and recommended bush hammering. The rougher
surface would provide a better bond for the Thoroseal. [93] During his next inspection, just a week before Richard
Neutra was expected at the site, Longstreth found the surface unacceptable.
He predicted that
the expression of the construction joints will telegraph
through the final finish particularly because of the irregularities
not in the surface between the ribs but of the ribs themselves which
cast elongated shadows to accentuate their irregularities. These occur
repeatedly at all construction joints and make a staccato shadow pattern
at each joint around the drum. Unless the patching of the ribbing
is perfect it is felt that this staccato pattern will show through
final finish. [94]
Even after a September visit from the EODC to address problems with
the application of Thoroseal, Superintendent Myers was still dissatisfied
with the exterior finish. Visible shadows and other defects obviously
compromised the effort to obtain a smooth concrete surface. Nevertheless,
the Superintendent promised that if the contractors could apply another
coat and achieve a surface similar to "the northern most of the 12-foot
experimental panels," he would accept the job. [95] Project supervisor Smith personally observed the painting
foreman, a subcontractor, apply three coatings of Thoroseal just north
of the approved northern-most panel. In a follow-up report, Smith described
unsightly build up and shadows in the new work. [96]
The Thoroseal problems appear to have been resolved by early December;
when Neutra visited the site, he reported the job "favorable and engaging."
[97] Most important to Neutra was the opportunity
to test lighting conditions, particularly in the exhibit spaces, and
color effects, both of which could only be properly evaluated on site.
At this point, exhibit frames and dioramas were complete enough for
paint analysis. Neutra's letter included a summary of qualities that
"obviously put this building outside of the common run of projects,"
such as the audiovisual system, "the installation of the gigantic painting,
the final testing of large dimensioned sliding and swinging doors, the
perfection of the finish metal work, intended for long lasting sightliness
without running upkeep, of roof viewing decks, etc." [98]
CONTINUED 